Extrusion Machines, Process & Requirement for Plant Set-up
- About
- Extrusion
Process - Applications of
Boundary Wall - Requirement to set up
Extrusion Plant - Machine
Specifications
Pre-Stressed, Precast Concrete Hollow Core Light / Heavy Duty Boundary Wall Panels.
Pre-stressed Precast concrete Hollow core Boundary wall or Compound wall & Supporting ‘H’ column are made by Concrete Extrusion machine & reinforced with Carbon steel wires, which works without the need of any Mould or Form work for production.
There are two types of Pre-stressed Precast Concrete Hollow Core Extruded Boundary Wall Panels & it’s Supporting ‘H’ Column: -
- Light-duty Boundary wall panel with suitable Supporting ‘H’ Column Size - Thickness 50 mm x 300 mm Width X 2 lane cast at a time per casting bed & Length can be cut as per requirement. Normally 7 feet are easy to lifted by 2 persons while installation.
Supporting ‘H’ Column Size 150 x 150mm with through & through Hole in the center for inserting, holding & fixing M. S. Angle for further extension of height with Barbed wires.
Lightweight Boundary wall panel machine also available in the following - Heavy-duty Boundary wall panel with suitable Supporting ‘H’ Column Size - Thickness of 50, 65, 75, 80, 90, 100 & 120mm & Width can be 500mm to 600mm & Length can be cut as per requirement. For installation you need crane as being heavy.
Supporting ‘H’ Column for Heavy Duty: -
(A) Supporting ‘H’ Column Size 180 X 200 mm with inter-changeable inserts to suit thickness of panels of 50 / 65 / 75 / 80mm,
(B) Supporting ‘H’ Column Size 180 X 280mm with inter-changeable inserts to suit thickness of panels of 90 / 100 / 120 mm thick with through & through Hole in the centre for inserting, holding & fixing M.S. Angle for further extension of height with Barbed wires.
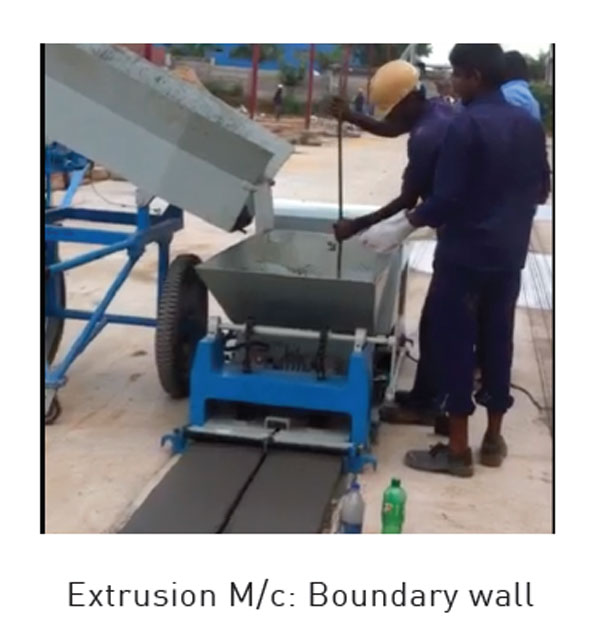
Brick walls, which have been traditional to India, is time consuming to erect and costly to keep maintaining. Our Pre-stressed Precast concrete Hollow core Boundary wall or Compound walls overcome these handicaps of traditional brick walls.
Extrusion of Boundary wall slab / panel is 5 times Faster, Easier & Most Economical solution for production compared to the conventional Technique of individual panel cast-in-situ.
Extrusion speed of the machine for the Light-duty Boundary wall slab is between 1.8 to 2 meters per Minute with a limited labour force. (i.e. it extrudes in one minute one panel of 7 feet). Being Hollow it’s self-weight is reduce, saves on concrete weight & thus save money with same load bearing capacity as compared with cast-in-situ.
Our Precast Concrete Boundary walls are made/ erected with the help of Supporting ‘H’ column / posts erected directly into the ground which have grooves to accommodate Boundary wall slabs / panels.
This can be also installed vertically without post as a boundary wall or cold storage rooms or industrial sheds, Pre-fabricated mezzanine floors etc.
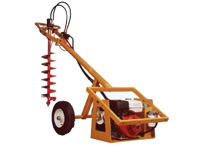
The Extrusion Process / Production cycle:-
The Extrusion process for Light-duty & Heavy-duty Boundary wall Panels & Supporting ‘H’ column (supporting post) is similar to above Pre-stressed Precast concrete Hollow core Light-weight Wall panel & Pre-stressed Precast concrete Hollow core Load bearing slab casting as given in our other projects. Even the other manufacturing process like, abutment of Carbon steel wire, curing, cutting, lifting & Storage is similar to our other projects.
Concrete beds prepared for Pre-stressed Precast concrete Hollow core Light-weight Wall panel are used for the light-duty Boundary Wall Panels & Supporting 'H' column or Vice versa.
The light-duty Boundary wall extrusion machine works with Augers / screws to extrude hollow core concrete slab of Good surface finish. After sufficient curing the slabs are cut to size & lifted & shifted to storage yards on trolleys manually being light-duty. The Heavy-duty Boundary wall extrusion machine works with pushing technology to extrude hollow core concrete slab.
Say on Day 1, if slab Extrusion is done on all 7 Lanes for Boundary wall panels. On Next / subsequent day they are Cut to size, lifted & floor is cleaned & prepared for subsequent / next day’s extrusion. In a month for 26 working days you Extrude Slab for panel or supporting column on alternate days i.e. 13 days Extrusion Ratio of Panel to Supporting Column is 85% : 15%. Hence Extrude 11 days slab for Panel & 2 days for supporting Column.
2 Nos. at a Time are extruded per lane for Boundary Wall Panels OR for Supporting Column. Each lane is of 260 feet long (80 Meters) but Effective production is 240 feet only. Production per day for Panel Or Supporting column is 240 ft x 2 cast / lane x 7 lanes x 90% efficiency = 3024 feet.
Zero Slump Concrete is used for Extrusion of above. Where Water Cement ration is just 0.3%. Extruder needs to be fed continuously with concrete hence we advice good Cylindrical Mixer & not Drum mixer. (Optional For High volume of Production you require Cement Silo & Batching & Dosing plant with Wheel loader.)
The Basic work flow for concrete Extrusion of slabs for Light-duty & Heavy-duty Boundary wall Panels or Supporting column i.e. ‘H’ / ‘I’ section is as follows:-
- Preparing the concrete platform / casting beds by cleaning & oiling.
- Carbon Steel wires are pulled from coils & placed for stressing (size as per length of bed) at Live end & Dead ends of the Casting platform.
- Pre-stress Carbon Steel wires with Stressing equipment.
- Prepare concrete mix using Cement, Sand, Aggregate & water of M20 or M25 grade in a Cylindrical Mixer.
- Using 2 nos. of Battery operated Mini Dumper / Manual cart Fill the hopper of Extruder m/c. with above Concrete mix into continuously.
- Run Extrusion m/c from one lane of casting to another lane as per instruction & cast slab around the Carbon Steel wires.
- Water the slab & then Cover it for Fast & better Curing.
- For Quality Check, Test block casted along with extrusion of slab is to be analysed.
- Once the slab is cured Mark & Cut with Slab cutting m/c to make panels or columns of required lengths as per order.
- Lift Panels or column & Move it form concrete platform for further Curing or storage or dispatch.
- In a dry climate, the stacks of Panels or column should be covered with plastic cover / tarpaulins.
- Clean & wash all the machine & equipment as per instruction.
- For more profit & to make it economical 2 Nos. are extruded at a Time per lane of Boundary Wall Panels OR Supporting Column. The extrusion speed of the machine is between 5 feet / 6 feet per minute. The Extrusion casting per lane will take around maximum 45 minutes depending on the length of the casting lane.
- Zero Slump Concrete is used for Extrusion, Where Water Cement ration is just 0.3%. As Extruder needs to be fed continuously with dry concrete, it is advisable to buy good Cylindrical Mixer & not Drum mixer.
- For High volume of Production you require Batching & Dosing Equipment & Cement Silo.
- To make it more economical you can add small portion of fly ash or foundry slag.
- The steel wires also help in the rigidity during loading, unloading, lifting and installation.
- List of machinery required: - Extrusion M/c for Panel - 1 No. + Extrusion M/c for Column -1 No. + Complete Concrete Mixer on stand & platform (i.e Cylindrical in shape & shaft rotating in horizontal plane) + Stressing M/c + Mini dumper / Manual Feeding Cart + Slab Cutting M/c + Dispensing stand for carbon steel wire + M/c lifting & shifting trolley.
Requirements for set-up to manufacture by Extrusion process Boundary Wall panels & Supporting 'H' Column
(if you wish to make boundary wall or sheds or rooms etc.)
- Land & Plant development:- About One Acre having length to width Ratio of 3:1. On this land make a well-level concrete platform by Land Filling, Compacting, Leveling & concreting with M25 grade of concrete etc (make similar to good quality of concrete Road) for extrusion of Wall Panels or supporting “H” columns.
- As per your land & quantity of production of panels & columns required by extrusion you can make Concrete platform (A) 260 feet long x 30 feet width for 7 lanes (B) 350 feet x 35 feet for 10 lanes. (C) 350 feet x 70 feet for 20 lanes.
- On the two ends of concrete platform need to fix / grout Abutment plates (lengthwise) for placing carbon steel wires of 3mm to 5mm dia. for reinforcement of panels or support column & stressing it. M.S. Steel Plate duly machined & drilled are used for Abutment as per out drawing.
- Balance land to be leveled & Paved for Mixer, Batching & dosing, Storage of sand & Aggregate,Storage of finished Goods, etc. + Office & Storage Room for cement or use Cement Silo plus requirements for Electrification, Drainage & Plumbing. (Please note: - For better efficiency on production more the length is better & less the wastage.)
- M.S. Steel flats to be grouted on the ground as per our design & drawing for Guiding Extrusion m/c. for straightness of slab.
- Testing & Quality Control:-Initially you can get it done outside in Test Lab. Then you can purchase Equipment:-Sieves & Sieve Shaker, Weighing Balance, Oven, Misc. Jars, Containers, Trays, Dryer, Impact Testing M/c, Compression Testing M/c (300 to 500 kN)
- Power Requirement: - Govt. power 20 KW or D.G. Set.
- Water Requirement: - Water Storage Tank: - 2000 Liters - 1 No for Plant, Office & Toilet. Water required Minimum 2,000 liters / day. (Free from salt)
Applications of Boundary Wall (Different names in market)
- Compound Wall
- RCC Boundary Wall
- Compound Boundary Wall
- Readymade Boundary Wall
- Precast Boundary Wall
- Precast Concrete Boundary Wall
- Precast Compound Wall
- Precast Concrete Compound Wall
- Cement Boundary Wall
- Prefabricated Boundary Wall
- Industrial Boundary Wall
- RCC Folding Boundary Wall
- RCC Pre-stressed Precast Boundary Wall
- RCC Compound Boundary Wall
- RCC Compound / Boundary Wall
- Precast Pre-stressed Boundary Walls
- Precast Pre-stressed Compound Wall
- Concrete Boundary Wall
- Concrete Compound Wall
- Fencing Wall
- Concrete Fencing Wall
- RCC Concrete Fencing Wall
- Precast Fencing Wall
- Pre-stressed, Precast Fencing Wall
- Fencing Wall made from concrete
- Garden Wall
- Boundary Walls for SEZ & large plants
- Office Building
- Portable Office Building
- Portable Office Cabin
- Potable Building
- Portable Office
- Site office
- Prefabricated Security Building
- Prefabricated Security Cabin
- Security Offices
- Security Shed
- Road Side Toilet Blocks
- Toilet blocks
- Labour Quarters / Labour Colony
- Labour Quarter
- Prefabricated Labour Quarter
- Portable Labour Quarter
- Industrial Sheds
- Animal Shed
- Godowns
- Ware houses
- Building Houses
- Garages
- Chowl
- Floorings
- Garden Curbing
- Foot Path Curbing
- Environment Friendly Project
- Fencing Pole – for H Column
- Concrete Fencing Pole – for H Column
- Vineyard Pillars
- Vineyard Posts.
Sr. No. | Model | Size of Slab (mm) | Power (kw) | Weight / meter (kg) | Remarks | Reinforcement of Slabs is with Carbon Tor Steel of 3mm Dia |
---|---|---|---|---|---|---|
1 | BW 50-300-1 |
Thickness - 50 Width - 300 |
1.35 | 30 | Cast 1 lane per Casting Bed | ![]() |
2 | BW 50-300-2 |
Thickness - 50 Width - 300 |
5.5 | 30 | Cast 2 lanes per Casting Bed | ![]() |
3 | BW 50-500 |
Thickness - 50 Width - 500 |
5.5 | 55 | Cast 1 lane per Casting Bed | ![]() |
4 | BW 80-500 |
Thickness - 80 Width - 500 |
5.5 | 75 | Cast 1 lane per Casting Bed | ![]() |
5 | BW 90-600 |
Thickness - 90 Width - 600 |
7.7 | 85 | Cast 1 lane per Casting Bed | ![]() |
6 | BW 100-600 |
Thickness - 100 Width - 600 |
7.7 | 98 | Cast 1 lane per Casting Bed | ![]() |